Dolné chemické vstrekovacie linky – prečo zlyhávajú?Skúsenosti, výzvy a aplikácie nových testovacích metód
Copyright 2012, Society of Petroleum Engineers
Abstraktné
Statoil prevádzkuje niekoľko oblastí, kde sa aplikuje kontinuálne vstrekovanie inhibítora vodného kameňa.Cieľom je chrániť hornú hadičku a poistný ventil pred (Ba/Sr) SO4 alebo CaCO;vodný kameň v prípadoch, keď môže byť ťažké a nákladné vykonávať pravidelné odstraňovanie vodného kameňa, napr. viazanie podmorských polí.
Kontinuálna injektáž inhibítora vodného kameňa dolu je technicky vhodným riešením na ochranu hornej hadičky a bezpečnostného ventilu vo vrtoch, ktoré majú potenciál tvorby vodného kameňa nad výrobným pakrom;najmä v vrtoch, ktoré nie je potrebné pravidelne stláčať kvôli potenciálu tvorby vodného kameňa v blízkosti vrtu.
Navrhovanie, prevádzka a údržba chemických vstrekovacích liniek si vyžaduje špeciálne zameranie na výber materiálu, chemickú kvalifikáciu a monitorovanie.Tlak, teplota, prietokové režimy a geometria systému môžu predstavovať problémy pre bezpečnú prevádzku.Problémy boli identifikované v niekoľko kilometrov dlhých vstrekovacích linkách od výrobného zariadenia po podmorskú šablónu a vo vstrekovacích ventiloch dole vo vrtoch.
Diskutuje sa o skúsenostiach v teréne, ktoré ukazujú zložitosť systémov kontinuálneho vstrekovania dole, pokiaľ ide o problémy so zrážaním a koróziou.Laboratórne štúdie a aplikácia nových metód pre chemickú kvalifikáciu a reprezentované.Riešia sa potreby multidisciplinárnych činností.
Úvod
Statoil prevádzkuje niekoľko oblastí, v ktorých sa používa kontinuálne vstrekovanie chemikálií.Ide hlavne o vstrekovanie inhibítora vodného kameňa (SI), kde cieľom je chrániť hornú hadičku a bezpečnostný ventil (DHSV) pred (Ba/Sr) SO4 alebo CaCO;stupnica.V niektorých prípadoch sa rozbíjač emulzie vstrekuje dole, aby sa začal separačný proces čo najhlbšie v studni pri relatívne vysokej teplote.
Kontinuálna injektáž inhibítora vodného kameňa dole je technicky vhodným riešením na ochranu hornej časti vrtov, ktoré majú potenciál tvorby vodného kameňa nad výrobným pakrom.Nepretržité vstrekovanie sa môže odporúčať najmä v vrtoch, ktoré nie je potrebné stláčať z dôvodu nízkeho potenciálu tvorby vodného kameňa v blízkom vrtu;alebo v prípadoch, keď môže byť pravidelné vykonávanie odstraňovania vodného kameňa zložité a nákladné, napr. pripájanie podmorských polí.
Statoil má rozsiahle skúsenosti s nepretržitým vstrekovaním chemikálií do systémov na vrchnej strane a podmorských šablón, ale novou výzvou je posunúť bod vstrekovania hlbšie do vrtu.Navrhovanie, prevádzka a údržba chemických vstrekovacích liniek si vyžaduje osobitné zameranie na niekoľko tém;ako je výber materiálu, chemická kvalifikácia a monitorovanie.Tlak, teplota, prietokové režimy a geometria systému môžu predstavovať problémy pre bezpečnú prevádzku.Boli identifikované problémy v dlhých (niekoľko kilometrov) vstrekovacích linkách z výrobného zariadenia do podmorskej šablóny a do vstrekovacích ventilov dole vo vrtoch;Obr.1.Niektoré vstrekovacie systémy fungovali podľa plánu, zatiaľ čo iné z rôznych dôvodov zlyhali.Plánuje sa niekoľko nových vývojov v oblasti chemického vstrekovania (DHCI);avšak;v niektorých prípadoch zariadenie ešte nebolo plne kvalifikované.
Aplikácia DHCI je komplexná úloha.Zahŕňa dokončenie a návrhy studní, chémiu studne, systém vrchnej strany a systém dávkovania chemikálií pri procese na vrchnej strane.Chemikália bude čerpaná z vrchnej strany cez chemickú vstrekovaciu linku do kompletizačného zariadenia a dole do vrtu.Preto je pri plánovaní a realizácii tohto typu projektu kľúčová spolupráca medzi viacerými disciplínami.Je potrebné zhodnotiť rôzne aspekty a dôležitá je dobrá komunikácia počas návrhu.Sú zapojení procesní inžinieri, podmorskí inžinieri a dokončovací inžinieri, ktorí sa zaoberajú témami chémie vrtov, výberom materiálu, zabezpečením toku a riadením výrobných chemikálií.Problémom môže byť stabilita chemickej pištole alebo teplotná stabilita, korózia av niektorých prípadoch vákuový efekt v dôsledku miestneho tlaku a prietoku v chemickom vstrekovacom potrubí.Okrem toho podmienky, ako je vysoký tlak, vysoká teplota, vysoká rýchlosť plynu, vysoký potenciál tvorby vodného kameňa,diaľkový pupočný a hlboký vstrekovací bod vo vrte dávajú rôzne technické výzvy a požiadavky na vstrekovanú chemikáliu a vstrekovací ventil.
Prehľad systémov DHCI inštalovaných v prevádzkach Statoil ukazuje, že skúsenosti neboli vždy úspešné Tabuľka 1. Plánuje sa však zlepšenie konštrukcie vstrekovania, chemická kvalifikácia, prevádzka a údržba.Výzvy sa líšia v závislosti od oblasti a problémom nie je nevyhnutne to, že samotný chemický vstrekovací ventil nefunguje.
Počas posledných rokov sa vyskytlo niekoľko problémov týkajúcich sa chemických vstrekovacích liniek.V tomto článku sú uvedené niektoré príklady z týchto skúseností.Článok pojednáva o výzvach a opatreniach prijatých na vyriešenie problémov súvisiacich s linkami DHCI.Uvádzajú sa dve anamnézy;jeden o korózii a jeden o chemickej pištoli kráľa.Diskutuje sa o skúsenostiach v teréne, ktoré ukazujú zložitosť systémov kontinuálneho vstrekovania dole, pokiaľ ide o problémy so zrážaním a koróziou.
Do úvahy sa berú aj laboratórne štúdie a aplikácia nových metód chemickej kvalifikácie;ako čerpať chemikáliu, potenciál a prevencia tvorby vodného kameňa, komplexná aplikácia zariadenia a ako chemikália ovplyvní vrchný systém, keď sa chemikália vyrába späť.Akceptačné kritériá pre chemickú aplikáciu zahŕňajú environmentálne problémy, účinnosť, skladovaciu kapacitu na vrchnej strane, rýchlosť čerpadla, či je možné použiť existujúce čerpadlo atď. Technické odporúčania musia byť založené na kompatibilite tekutín a chémie, detekcii zvyškov, kompatibilite materiálu, podmorskom umbilikálnom dizajne, systéme dávkovania chemikálií a materiály v okolí týchto liniek.Chemikáliu môže byť potrebné inhibovať hydrátom, aby sa zabránilo upchatiu vstrekovacieho potrubia inváziou plynu a chemikália nesmie zamrznúť počas prepravy a skladovania.V existujúcich interných smerniciach je zoznam chemikálií, ktoré možno použiť v každom bode systému. Dôležité sú fyzikálne vlastnosti, ako je viskozita.Injekčný systém môže znamenať vzdialenosť 3-50 km od pupočnej podmorskej línie toku a 1-3 km dole do vrtu.Preto je dôležitá aj teplotná stabilita.Možno bude potrebné zvážiť aj hodnotenie následných účinkov, napr. v rafinériách.
Systémy chemického vstrekovania
Nákladová výhoda
Nepretržité vstrekovanie inhibítora vodného kameňa do otvoru na ochranu DHS Pred výrobným potrubím môže byť nákladovo efektívne v porovnaní s vytláčaním jamky inhibítorom vodného kameňa.Táto aplikácia znižuje možnosť poškodenia tvorby v porovnaní s úpravami vytláčaním vodného kameňa, znižuje možnosť problémov s procesom po vytláčaní šupín a dáva možnosť kontrolovať rýchlosť vstrekovania chemikálií z vrchného vstrekovacieho systému.Vstrekovací systém sa môže použiť aj na nepretržité vstrekovanie iných chemikálií dolu a môže tak znížiť ďalšie problémy, ktoré by sa mohli vyskytnúť ďalej v smere výrobného závodu.
Uskutočnila sa komplexná štúdia, ktorá vyvinula stratégiu klesajúcej škály poľa Oseberg S alebo pole.Hlavným problémom bol CaCO;tvorba vodného kameňa v hornej hadici a možné zlyhanie DHSV.Úvahy o stratégii riadenia Oseberg S alebo stupnice dospeli k záveru, že počas trojročného obdobia bol DHCI nákladovo najefektívnejším riešením v vrtoch, kde fungovali chemické vstrekovacie linky.Hlavným nákladovým prvkom v súvislosti s konkurenčnou technikou odstraňovania vodného kameňa bola skôr odložená ropa než chemické/prevádzkové náklady.Pri aplikácii inhibítora vodného kameňa pri zdvíhaní plynu bola hlavným faktorom nákladov na chemikálie vysoká rýchlosť zdvihu plynu, ktorá viedla k vysokej koncentrácii SI, pretože koncentrácia musela byť v rovnováhe s rýchlosťou zdvihu plynu, aby sa predišlo kráľovi chemickej pištole.Pre dve studne na Oseberg S alebo tie, ktoré mali dobre fungujúce vedenia DHC I, bola táto možnosť zvolená na ochranu DHS V proti CaCO;škálovanie.
Systém kontinuálneho vstrekovania a ventily
Existujúce dokončovacie riešenia využívajúce kontinuálne chemické vstrekovacie systémy čelia problémom, ako zabrániť upchávaniu kapilárnych vedení.Typicky vstrekovací systém pozostáva z kapilárneho vedenia s vonkajším priemerom (OD) 1/4” alebo 3/8” pripojeného k povrchovému rozdeľovaču, vedené cez a pripojené k závesu hadičky na prstencovej strane hadičky.Kapilárna linka je pripevnená k vonkajšiemu priemeru výrobnej hadičky špeciálnymi hadicovými golierovými svorkami a vedie na vonkajšej strane hadičky až po chemický vstrekovací tŕň.Tŕň sa tradične umiestňuje pred DHS V alebo hlbšie do vrtu s úmyslom poskytnúť vstrekovanej chemikálii dostatočný čas na disperziu a umiestniť chemikáliu tam, kde sa nachádzajú výzvy.
Na chemickom vstrekovacom ventile, obr. 2, malá náplň s priemerom asi 1,5” obsahuje spätné ventily, ktoré zabraňujú vnikaniu kvapalín z vrtu do kapilárneho potrubia.Je to jednoducho malá bábika jazdiaca na pružine.Sila pružiny nastavuje a predpovedá tlak potrebný na otvorenie taniera z tesniaceho sedla.Keď chemikália začne prúdiť, tanier sa zdvihne zo sedla a otvorí spätný ventil.
Vyžaduje sa inštalácia dvoch spätných ventilov.Jeden ventil je primárna bariéra, ktorá bráni vnikaniu tekutín z vrtu do kapilárneho potrubia.Toto má relatívne nízky otvárací tlak (2-15 barov). Ak je hydrostatický tlak vo vnútri kapilárneho potrubia nižší ako tlak vo vrtu, kvapaliny z vrtu sa pokúsia dostať do kapilárneho potrubia.Druhý spätný ventil má atypický otvárací tlak 130-250 barov a je známy ako systém prevencie U-trubice.Tento ventil bráni chemikálii vo vnútri kapilárneho potrubia voľne prúdiť do vrtu, ak by hydrostatický tlak vo vnútri kapilárneho potrubia bol väčší ako tlak vrtu v mieste vstrekovania chemikálie vo vnútri produkčného potrubia.
Okrem dvoch spätných ventilov je tu bežne in-line filter, ktorého účelom je zabezpečiť, aby žiadne nečistoty akéhokoľvek druhu nemohli ohroziť tesniace schopnosti systémov spätných ventilov.
Veľkosti opísaných spätných ventilov sú pomerne malé a čistota vstrekovanej kvapaliny je nevyhnutná pre ich prevádzkovú funkčnosť.Predpokladá sa, že úlomky v systéme môžu byť odplavené zvýšením prietoku vo vnútri kapilárneho potrubia, takže spätné ventily sa svojvoľne otvoria.
Keď sa spätný ventil otvorí, prietokový tlak rýchlo klesá a šíri sa hore kapilárnym vedením, kým sa tlak opäť nezvýši.Spätný ventil sa potom zatvorí, kým tok chemikálií nevytvorí dostatočný tlak na otvorenie ventilu;výsledkom sú kolísanie tlaku v systéme spätného ventilu.Čím vyšší otvárací tlak má systém spätného ventilu, tým menšia prietoková plocha sa vytvorí, keď sa spätný ventil otvorí a systém sa snaží dosiahnuť rovnovážne podmienky.
Chemické vstrekovacie ventily majú relatívne nízky otvárací tlak;a ak sa tlak v hadičke v bode vstupu chemikálie zníži ako súčet hydrostatického tlaku chemikálií vo vnútri kapilárneho vedenia plus otvárací tlak spätného ventilu, v hornej časti kapilárneho vedenia sa objaví takmer vákuum alebo vákuum.Keď sa vstrekovanie chemikálie zastaví alebo je prietok chemikálie nízky, v hornej časti kapilárneho vedenia sa začnú objavovať podmienky blízke vákuu.
Úroveň vákua závisí od tlaku vo vrte, špecifickej hmotnosti vstrekovanej chemickej zmesi použitej vo vnútri kapilárneho potrubia, otváracieho tlaku spätného ventilu v mieste vstrekovania a prietoku chemikálie vo vnútri kapilárneho potrubia.Podmienky vrtu sa budú počas životnosti poľa meniť a potenciál pre vákuum sa preto bude meniť aj v priebehu času.Je dôležité si uvedomiť túto situáciu, aby ste správne zvážili a vykonali preventívne opatrenia skôr, ako sa vyskytnú očakávané problémy.
Spolu s nízkymi rýchlosťami vstrekovania sa zvyčajne rozpúšťadlá používané v týchto typoch aplikácií vyparujú a spôsobujú účinky, ktoré neboli úplne preskúmané.Tieto efekty sú gun king alebo zrážanie pevných látok, napríklad polymérov, keď sa rozpúšťadlo odparuje.
Ďalej, galvanické články môžu byť vytvorené v prechodovej fáze medzi povrchom tekutiny chemikálie a plynnou fázou naplnenou parami v blízkosti vákua vyššie.To môže viesť k lokálnej bodovej korózii vo vnútri kapilárneho vedenia v dôsledku zvýšenej agresivity chemikálie za týchto podmienok.Vločky alebo kryštály soli vytvorené ako film vo vnútri kapilárnej línie, keď sa jej vnútro vysychá, môžu upchať alebo upchať kapiláru.
Filozofia bariéry
Pri navrhovaní robustných riešení vrtu Statoil vyžaduje, aby bola bezpečnosť vrtu na mieste vždy počas životného cyklu vrtu.Statoil teda vyžaduje, aby existovali dve nezávislé neporušené bariéry studní.Obr. 3 zobrazuje atypickú schému bariéry studne, kde modrá farba predstavuje obal primárnej bariéry studne;v tomto prípade výrobné potrubie.Červená farba predstavuje sekundárny bariérový obal;puzdro.Na ľavej strane v náčrte je chemická injekcia označená ako čierna čiara s bodom vstrekovania do výrobného potrubia v oblasti označenej červenou farbou (sekundárna bariéra).Zavedením chemických vstrekovacích systémov do vrtu sú ohrozené primárne aj sekundárne bariéry vrtu.
Prípad korózie
Postupnosť udalostí
Do ropného poľa prevádzkovaného spoločnosťou Statoil na nórskom kontinentálnom šelfe bola aplikovaná dolná chemická injekcia inhibítora vodného kameňa.V tomto prípade použitý inhibítor vodného kameňa bol pôvodne kvalifikovaný na použitie na vrchnej a podmorskej ploche.Po opätovnom dokončení vrtu nasledovala inštalácia DHCIpointat2446mMD, obr.3.Injektáž inhibítora vodného kameňa na vrchnej strane sa začala bez ďalšieho testovania chemikálie.
Po roku prevádzky boli pozorované netesnosti v chemickom vstrekovacom systéme a začali sa vyšetrovania.Únik mal škodlivý vplyv na bariéry studní.Podobné udalosti sa vyskytli pri niekoľkých vrtoch a niektoré z nich museli byť počas vyšetrovania uzavreté.
Výrobné potrubie bolo vytiahnuté a podrobne preštudované.Napadnutie koróziou bolo obmedzené na jednu stranu potrubia a niektoré spoje potrubia boli tak skorodované, že cez ne boli v skutočnosti otvory.Približne 8,5 mm hrubá 3% chrómová oceľ sa rozpadla za menej ako 8 mesiacov.Hlavná korózia sa vyskytla v hornej časti vrtu, od ústia vrtu nadol po približne 380 m MD, a najhoršie skorodované spoje rúrok sa našli vo výške približne 350 m MD.Pod touto hĺbkou bola pozorovaná malá alebo žiadna korózia, ale na vonkajších okrajoch hadičiek sa našlo veľa úlomkov.
Puzdro 9-5/8'' bolo tiež narezané a vytiahnuté a boli pozorované podobné účinky;s koróziou v hornej časti studne len na jednej strane.Indukovaný únik bol spôsobený prasknutím oslabenej časti plášťa.
Materiál chemického vstrekovacieho potrubia bola zliatina 825.
Chemická kvalifikácia
Chemické vlastnosti a testovanie korózie sú dôležitým zameraním pri kvalifikácii inhibítorov vodného kameňa a skutočný inhibítor vodného kameňa bol kvalifikovaný a používaný v aplikáciách na vrchu a v podmorí už niekoľko rokov.Dôvodom na použitie skutočného chemického dolného otvoru boli zlepšené environmentálne vlastnosti nahradením existujúceho dolného otvoru. Inhibítor vodného kameňa sa však používal iba pri okolitých teplotách na povrchu a morskom dne (4-20 °C).Pri vstreknutí do studne mohla byť teplota chemikálie až 90 °C, ale pri tejto teplote sa nevykonali žiadne ďalšie testy.
Počiatočné testy korózie boli vykonané dodávateľom chemikálií a výsledky ukázali 2-4 mm/rok pre uhlíkovú oceľ pri vysokej teplote.V tejto fáze došlo k minimálnemu zapojeniu vecne technickej spôsobilosti prevádzkovateľa.Operátor neskôr vykonal nové testy, ktoré ukázali, že inhibítor vodného kameňa bol vysoko korozívny pre materiály vo výrobnom potrubí a výrobnom plášti s rýchlosťou korózie presahujúcou 70 mm/rok.Materiál chemického vstrekovacieho potrubia Alloy 825 nebol pred vstrekovaním testovaný proti inhibítoru vodného kameňa.Teplota studne môže dosiahnuť 90 ℃ a za týchto podmienok by sa mali vykonať primerané testy.
Skúmanie tiež odhalilo, že inhibítor vodného kameňa ako koncentrovaný roztok vykazoval pH < 3,0.pH však nebolo merané.Neskôr namerané pH ukázalo veľmi nízku hodnotu pH 0-1.To ilustruje potrebu meraní a materiálových úvah okrem daných hodnôt pH.
Interpretácia výsledkov
Vstrekovacie potrubie (obr. 3) je konštruované tak, aby poskytovalo hydrostatický tlak inhibítora vodného kameňa, ktorý prevyšuje tlak v mieste vstrekovania.Inhibítor sa vstrekuje pri vyššom tlaku, ako existuje vo vrte.Výsledkom je efekt U-rúrky pri uzavretí vrtu.Ventil sa vždy otvorí s vyšším tlakom vo vstrekovacom potrubí ako v studni.Vo vstrekovacom potrubí môže preto dôjsť k podtlaku alebo odparovaniu.Rýchlosť korózie a riziko jamkovej korózie je najväčšie v zóne prechodu plyn/kvapalina v dôsledku odparovania rozpúšťadla.Laboratórne experimenty vykonané na kupónoch túto teóriu potvrdili.Vo vrtoch, kde došlo k úniku, boli všetky otvory vo vstrekovacích potrubiach umiestnené v hornej časti chemického vstrekovacieho potrubia.
Obr. 4 ukazuje fotografiu línie DHC I s výraznou bodovou koróziou.Korózia pozorovaná na vonkajšom výrobnom potrubí indikovala lokálnu expozíciu inhibítora vodného kameňa z miesta bodového úniku.Únik bol spôsobený jamkovou koróziou vysoko korozívnou chemikáliou a únikom cez chemickú vstrekovaciu linku do výrobného plášťa.Inhibítor vodného kameňa bol nastriekaný z jamkovej kapilárnej línie na puzdro a hadičku a došlo k netesnostiam.Akékoľvek sekundárne dôsledky netesností vo vstrekovacom potrubí neboli zohľadnené.Dospelo sa k záveru, že korózia plášťa a hadičky bola výsledkom koncentrovaných inhibítorov vodného kameňa vynášaných z jamkovej kapiláry na plášť a hadičku, obr.
V tomto prípade chýbalo zapojenie inžinierov materiálovej kompetencie.Korozívnosť chemikálie na vedení DHCI nebola testovaná a sekundárne účinky spôsobené únikom neboli hodnotené;ako napríklad či by okolité materiály mohli tolerovať vystavenie chemikáliám.
Prípad kráľa chemických zbraní
Postupnosť udalostí
Stratégiou prevencie tvorby vodného kameňa pre pole HP HT bolo nepretržité vstrekovanie inhibítora vodného kameňa pred bezpečnostným ventilom v zvode.V studni bol identifikovaný silný potenciál usadzovania uhličitanu vápenatého.Jednou z výziev bola vysoká teplota a vysoká rýchlosť produkcie plynu a kondenzátu v kombinácii s nízkou rýchlosťou produkcie vody.Pri vstrekovaní inhibítora vodného kameňa išlo o to, že pri vysokej rýchlosti produkcie plynu by sa rozpúšťadlo odstránilo a v mieste vstrekovania pred bezpečnostným ventilom vo vrte by sa vyskytla pištoľ proti prúdu chemikálie, obr.
Počas kvalifikácie inhibítora vodného kameňa sa pozornosť sústredila na účinnosť produktu v podmienkach HP HT vrátane správania sa v hornom procesnom systéme (nízka teplota).Hlavným problémom bolo vyzrážanie samotného inhibítora vodného kameňa vo výrobnom potrubí v dôsledku vysokej rýchlosti plynu.Laboratórne testy ukázali, že inhibítor vodného kameňa sa môže vyzrážať a priľnúť k stene hadičky.Prevádzka poistného ventilu preto môže prekonať riziko.
Prax ukázala, že po niekoľkých týždňoch prevádzky chemická linka presakovala.Tlak vo vrte bolo možné monitorovať na hladinomere inštalovanom v kapilárnom potrubí.Línia bola izolovaná, aby sa získala integrita jamky.
Chemické vstrekovacie vedenie bolo vytiahnuté z vrtu, otvorené a skontrolované, aby sa diagnostikoval problém a našli sa možné príčiny zlyhania.Ako je možné vidieť na obr. 6, našlo sa významné množstvo zrazeniny a chemická analýza ukázala, že časť z nich bola inhibítorom vodného kameňa.Zrazenina sa nachádzala na tesnení a tanier a ventil sa nedali ovládať.
Porucha ventilu bola spôsobená úlomkami vo vnútri ventilového systému, ktoré bránia spätným ventilom pohlcovať sedlo z kovu na kov.Nečistoty boli preskúmané a ukázalo sa, že hlavnými časticami sú kovové hobliny, pravdepodobne vytvorené počas procesu inštalácie kapilárneho vedenia.Okrem toho bolo na oboch spätných ventiloch identifikovaných niekoľko bielych nečistôt, najmä na zadnej strane ventilov.Toto je strana s nízkym tlakom, tj strana by bola vždy v kontakte s kvapalinami z vrtu.Spočiatku sa predpokladalo, že ide o úlomky z produkčného vrtu, pretože ventily boli zaseknuté otvorené a vystavené kvapalinám z vrtu.Pri skúmaní sa však ukázalo, že úlomky sú polyméry s podobnou chémiou ako chemikália používaná ako inhibítor vodného kameňa.To nás zaujalo a Statoil chcel preskúmať dôvody týchto polymérnych zvyškov prítomných v kapilárnej línii.
Chemická kvalifikácia
V oblasti HP HT existuje veľa výziev, pokiaľ ide o výber vhodných chemikálií na zmiernenie rôznych výrobných problémov.Pri kvalifikácii inhibítora vodného kameňa pre kontinuálne vstrekovanie dolu boli vykonané tieto testy:
● Stabilita produktu
● Tepelné starnutie
● Dynamické výkonnostné testy
● Kompatibilita s tvorbou vody a inhibítorom hydratácie (MEG)
● Statický a dynamický test kráľa pištole
● Informačná voda o opätovnom rozpustení, čerstvé chemikálie a MEG
Chemikália sa vstrekne vopred stanovenou rýchlosťou dávky,ale produkcia vody nebude nevyhnutne konštantná,tj hromadenie vody.Medzi vodnými slimákmi,keď sa chemikália dostane do vrtu,stretne ho horúca,rýchlo prúdiaci prúd uhľovodíkového plynu.Je to podobné ako pri vstrekovaní inhibítora vodného kameňa v aplikácii plynového výťahu (Fleming a kol. 2003).
vysoká teplota plynu,riziko stripovania rozpúšťadla je extrémne vysoké a pištoľ môže spôsobiť zablokovanie vstrekovacieho ventilu.Toto je riziko aj pre chemikálie formulované s rozpúšťadlami s vysokým bodom varu/nízkym tlakom pár a inými látkami znižujúcimi tlak pár (VPD). V prípade čiastočného zablokovania,prúdenie formačnej vody,MEG a/alebo čerstvá chemikália musia byť schopné odstrániť alebo znovu rozpustiť dehydratovanú alebo vysypanú chemikáliu.
V tomto prípade bolo navrhnuté nové laboratórne testovacie zariadenie na replikáciu podmienok prúdenia v blízkosti vstrekovacích otvorov vo výrobnom systéme HP/HTg.Výsledky dynamických testov pištole ukazujú, že pri navrhovaných podmienkach použitia bola zaznamenaná významná strata rozpúšťadla.To by mohlo viesť k rýchlemu ovládaniu pištole a prípadnému zablokovaniu prietokových potrubí.Práca preto preukázala, že existovalo relatívne významné riziko pre nepretržité vstrekovanie chemikálií do týchto vrtov pred výrobou vody a viedlo k rozhodnutiu upraviť bežné postupy spúšťania pre túto oblasť, čím sa oddialilo vstrekovanie chemikálií, kým sa nezistí prienik vody.
Kvalifikácia inhibítora vodného kameňa pre kontinuálne vstrekovanie dolu mala veľký dôraz na odstraňovanie rozpúšťadla a pištoľový uzáver inhibítora vodného kameňa v mieste vstrekovania a v prietokovom potrubí, ale potenciál pre pištoľ v samotnom vstrekovacom ventile nebol hodnotený.Vstrekovací ventil pravdepodobne zlyhal v dôsledku výraznej straty rozpúšťadla a rýchleho kráľa pištole,Obr.6. Výsledky ukazujú, že je dôležité mať na systém holistický pohľad;zamerať sa nielen na výrobné výzvy,ale aj problémy súvisiace so vstrekovaním chemikálie,tj vstrekovací ventil.
Skúsenosti z iných oblastí
Jedna z prvých správ o problémoch s potrubím pre chemické vstrekovanie na veľké vzdialenosti bola zo satelitných polí Gull fak sandVig dis (Osa a kol. 2001). Podmorské vstrekovacie potrubia boli zablokované pred tvorbou hydrátov v potrubí v dôsledku invázie plynu z vyrábaných tekutín. do potrubia cez vstrekovací ventil.Boli vyvinuté nové usmernenia pre vývoj chemikálií na podmorskú výrobu.Požiadavky zahŕňali odstránenie častíc (filtráciu) a pridanie hydrátového inhibítora (napr. glykolu) ku všetkým inhibítorom vodného kameňa na báze vody, ktoré sa majú vstrekovať do podmorských šablón.Chemická stabilita,Zohľadnila sa aj viskozita a kompatibilita (kvapalina a materiály).Tieto požiadavky boli prebraté ďalej do systému Statoil a zahŕňajú vstrekovanie chemikálií dole.
Počas vývojovej fázy Oseberg S alebo poľa sa rozhodlo, že všetky vrty by mali byť doplnené systémami DHC I (Fleming a kol. 2006). Cieľom bolo zabrániť CaCO;škálovanie v hornej hadici vstrekovaním SI.Jednou z hlavných výziev v súvislosti s chemickými vstrekovacími linkami bolo dosiahnutie komunikácie medzi povrchom a výstupom z vleku.Vnútorný priemer chemického vstrekovacieho potrubia sa zúžil zo 7 mm na 0,7 mm (ID) okolo prstencového bezpečnostného ventilu v dôsledku priestorových obmedzení a schopnosť kvapaliny transportovať cez túto sekciu ovplyvnila mieru úspešnosti.Niekoľko plošinových vrtov malo chemické vstrekovacie potrubia, ktoré boli upchaté,ale dôvod nebol pochopený.Vlaky rôznych tekutín (glykol,hrubý,kondenzát,xylén,inhibítor vodného kameňa,voda atď.) boli laboratórne testované na viskozitu a kompatibilitu a čerpali sa dopredu a v opačnom smere, aby sa potrubia otvorili;však,cieľový inhibítor vodného kameňa nebolo možné prečerpať až po ventil vstrekovania chemikálií.Ďalej,komplikácie boli pozorované pri precipitácii fosfonátového inhibítora vodného kameňa spolu so zvyškovým CaClz kompletným soľným roztokom v jednej studni a pištoľovým kráľom inhibítora vodného kameňa vo vnútri studne s vysokým pomerom plynového oleja a nízkym obsahom vody (Fleming et al. 2006).
Ponaučenie
Vývoj skúšobnej metódy
Hlavné ponaučenia zo zlyhania systémov DHC I sa týkali technickej účinnosti inhibítora vodného kameňa a nie funkčnosti a chemického vstrekovania.Horná injekcia a podmorská injekcia fungovali dobre nadčas;však,aplikácia bola rozšírená na hĺbkové vstrekovanie chemikálií bez zodpovedajúcej aktualizácie metód chemickej kvalifikácie.Skúsenosti Statoil z dvoch prezentovaných terénnych prípadov sú také, že riadiaca dokumentácia alebo usmernenia pre chemickú kvalifikáciu musia byť aktualizované, aby zahŕňali tento typ chemickej aplikácie.Hlavné dve výzvy boli identifikované ako i) vákuum v chemickom vstrekovacom potrubí a ii) potenciálne vyzrážanie chemikálie.
K odparovaniu chemikálie môže dôjsť na výrobnom potrubí (ako je vidieť na puzdre pištole) a vo vstrekovacom potrubí (vo vákuovom puzdre bolo identifikované prechodné rozhranie), existuje riziko, že tieto precipitáty sa môžu pohybovať prúdom a do vstrekovacieho ventilu a ďalej do vrtu.Vstrekovací ventil je často navrhnutý s filtrom pred bodom vstrekovania,toto je výzva,pretože v prípade zrážok môže byť tento filter upchatý, čo spôsobí zlyhanie ventilu.
Pozorovania a predbežné závery zo získaných poznatkov viedli k rozsiahlej laboratórnej štúdii javov.Celkovým cieľom bolo vyvinúť nové kvalifikačné metódy, aby sa predišlo podobným problémom v budúcnosti.V tejto štúdii boli vykonané rôzne testy a bolo navrhnutých niekoľko laboratórnych metód (vyvinutých za účelom) na skúmanie chemikálií s ohľadom na identifikované problémy.
● Upchatie filtra a stabilita produktu v uzavretých systémoch.
● Vplyv čiastočnej straty rozpúšťadla na korozívnosť chemikálií.
● Vplyv čiastočnej straty rozpúšťadla v kapiláre na tvorbu pevných látok alebo viskóznych zátok.
Počas testov laboratórnych metód bolo identifikovaných niekoľko potenciálnych problémov
● Opakované upchatie filtra a slabá stabilita.
● Tvorba pevných látok po čiastočnom odparení z kapiláry
● Zmeny pH v dôsledku straty rozpúšťadla.
Povaha vykonaných testov tiež poskytla ďalšie informácie a poznatky týkajúce sa zmien fyzikálnych vlastností chemikálií v kapilárach, keď sú vystavené určitým podmienkam,a ako sa to líši od objemových roztokov vystavených podobným podmienkam.Skúšobná práca tiež identifikovala značné rozdiely medzi objemovou kvapalinou,parné fázy a zvyškové kvapaliny, čo môže viesť buď k zvýšenému potenciálu zrážania a/alebo zvýšenej korozívnosti.
Skúšobný postup pre korozívnosť inhibítorov vodného kameňa bol vyvinutý a zahrnutý do riadiacej dokumentácie.Pre každú aplikáciu bolo potrebné vykonať rozšírené testovanie korozívnosti predtým, ako bolo možné implementovať injekciu inhibítora vodného kameňa.Uskutočnili sa aj testy Gun King chemikálie vo vstrekovacej linke.
Pred začatím kvalifikácie chemikálie je dôležité vytvoriť rozsah práce, ktorý popisuje výzvy a účel chemikálie.V počiatočnej fáze je dôležité identifikovať hlavné problémy, aby ste mohli vybrať typy chemikálií, ktoré vyriešia problém.Súhrn najdôležitejších kritérií prijatia nájdete v tabuľke 2.
Kvalifikácia chemikálií
Kvalifikácia chemikálií pozostáva z testovania a teoretických hodnotení pre každú aplikáciu.Je potrebné definovať a stanoviť technické špecifikácie a testovacie kritériá,napríklad v rámci HSE,materiálová kompatibilita,stabilita produktu a kvalita produktu (častice).Ďalej,bod mrazu,viskozita a kompatibilita s inými chemikáliami,hydrátový inhibítor,treba určiť formovaciu vodu a produkovanú tekutinu.Zjednodušený zoznam testovacích metód, ktoré možno použiť na kvalifikáciu chemikálií, je uvedený v tabuľke 2.
Neustále zameranie a sledovanie technickej efektívnosti,dávky a fakty o HSE sú dôležité.Požiadavky na produkt môžu zmeniť oblasť alebo životnosť výrobného závodu;líšia sa rýchlosťou výroby, ako aj zložením tekutiny.Následná činnosť s hodnotením výkonu,optimalizácia a/alebo testovanie nových chemikálií sa musí vykonávať často, aby sa zabezpečil optimálny program úpravy.
V závislosti od kvality oleja,výroba vody a technické výzvy vo výrobnom závode na mori,použitie výrobných chemikálií môže byť nevyhnutné na dosiahnutie exportnej kvality,regulačné požiadavky,a prevádzkovať pobrežné zariadenie bezpečným spôsobom.Všetky oblasti majú rôzne výzvy a potrebné výrobné chemikálie sa budú líšiť v závislosti od oblasti a nadčasov.
V kvalifikačnom programe je dôležité zamerať sa na technickú efektívnosť výrobných chemikálií,ale je tiež veľmi dôležité zamerať sa na vlastnosti chemikálie,ako je stabilita,kvalitu a kompatibilitu produktu.Kompatibilita v tomto nastavení znamená kompatibilitu s kvapalinami,materiály a iné výrobné chemikálie.To môže byť výzva.Nie je žiaduce použiť chemikáliu na vyriešenie problému, aby sa neskôr zistilo, že chemikália prispieva k novým výzvam alebo vytvára nové výzvy.Najväčšou výzvou sú možno vlastnosti chemikálie a nie technická výzva.
Špeciálne požiadavky
Špeciálne požiadavky na filtráciu dodávaných produktov by sa mali vzťahovať na podmorský systém a na kontinuálne vstrekovanie dole.Sitá a filtre v systéme chemického vstrekovania by mali byť k dispozícii na základe špecifikácie zariadenia nadväzujúceho na vstrekovací systém na hornej strane,čerpadlá a vstrekovacie ventily,k vstrekovacím ventilom do dolného otvoru.Tam, kde sa používa kontinuálne vstrekovanie chemikálií dole, špecifikácia v systéme chemického vstrekovania by mala byť založená na špecifikácii s najvyššou kritickosťou.Toto môže byť filter na vstrekovacom ventile dole.
Injekčné problémy
Injekčný systém môže znamenať vzdialenosť 3-50 km od pupočnej podmorskej toku a 1-3 km dole do vrtu.Dôležité sú fyzikálne vlastnosti, ako je viskozita a schopnosť čerpať chemikálie.Ak je viskozita pri teplote morského dna príliš vysoká, môže byť náročné prečerpať chemikáliu potrubím na vstrekovanie chemikálií v podmorskej umbilikáli a do bodu podmorskej injekcie alebo do vrtu.Viskozita by mala zodpovedať špecifikácii systému pri očakávanej skladovacej alebo prevádzkovej teplote.Toto by sa malo posúdiť v každom prípade,a bude závisieť od systému.Podľa tabuľky rýchlosť vstrekovania chemikálií je faktorom úspechu pri vstrekovaní chemikálií.Aby sa minimalizovalo riziko upchatia potrubia na vstrekovanie chemikálií,chemikálie v tomto systéme by mali byť inhibované hydrátmi (ak je potenciál pre hydráty).Musí sa overiť kompatibilita s kvapalinami prítomnými v systéme (konzervačná kvapalina) a inhibítorom hydrátov.Testy stability chemikálie pri skutočných teplotách (najnižšia možná teplota okolia,teplota okolia,podmorská teplota,teplota vstrekovania) musí prejsť.
Musí sa zvážiť aj program na umývanie potrubí vstrekovania chemikálií pri danej frekvencii.Pravidelné preplachovanie chemického vstrekovacieho potrubia rozpúšťadlom môže poskytnúť preventívny účinok,glykol alebo čistiacu chemikáliu, aby ste odstránili prípadné usadeniny skôr, než sa nahromadia a môžu spôsobiť upchatie vedenia.Zvolený chemický roztok preplachovacej kvapaliny musí byťkompatibilný s chemikáliou vo vstrekovacom potrubí.
V niektorých prípadoch sa chemická vstrekovacia linka používa na niekoľko chemických aplikácií založených na rôznych výzvach počas životnosti v teréne a podmienkach kvapalín.V počiatočnej produkčnej fáze pred prienikom vody môžu byť hlavné výzvy odlišné od tých, ktoré sú v neskoršom veku, ktoré často súvisia so zvýšenou produkciou vody.Prechod z inhibítora na báze nevodného rozpúšťadla, ako je inhibítor asfaltového énu, na chemikáliu na báze vody, ako je inhibítor vodného kameňa, môže spôsobiť problémy s kompatibilitou.Preto je dôležité zamerať sa na kompatibilitu a kvalifikáciu a použitie dištančných vložiek, keď sa plánuje výmena chemikálie v chemickej vstrekovacej linke.
Materiály
Čo sa týka materiálovej kompatibility,všetky chemikálie by mali byť kompatibilné s tesneniami,elastoméry,tesnenia a konštrukčné materiály používané v systéme chemického vstrekovania a vo výrobnom závode.Mal by sa vypracovať skúšobný postup na žieravosť chemikálií (napr. kyslý inhibítor vodného kameňa) pre kontinuálne vstrekovanie dole.Pre každú aplikáciu je potrebné pred zavedením vstrekovania chemikálií vykonať rozšírené testovanie korózie.
Diskusia
Je potrebné vyhodnotiť výhody a nevýhody kontinuálneho dolného chemického vstrekovania.Nepretržité vstrekovanie inhibítora vodného kameňa na ochranu DHS Vor produkčné potrubie je elegantný spôsob ochrany studne pred vodným kameňom.Ako je uvedené v tomto dokumente, existuje niekoľko problémov s kontinuálnym vstrekovaním chemikálií,avšak na zníženie rizika je dôležité pochopiť javy spojené s riešením.
Jedným zo spôsobov, ako znížiť riziko, je zamerať sa na vývoj testovacích metód.V porovnaní s hornou alebo podmorskou chemickou injekciou sú dole v studni iné a závažnejšie podmienky.Kvalifikačný postup pre chemikálie na kontinuálne vstrekovanie chemikálií dole musí brať do úvahy tieto zmeny podmienok.Kvalifikácia chemikálií musí byť vykonaná podľa materiálu, s ktorým by sa chemikálie mohli dostať do kontaktu.Požiadavky na kvalifikáciu a testovanie kompatibility v podmienkach, ktoré čo najbližšie kopírujú rôzne podmienky životného cyklu vrtu, za ktorých budú tieto systémy fungovať, sa musia aktualizovať a implementovať.Vývoj skúšobnej metódy sa musí ďalej rozvíjať k realistickejším a reprezentatívnejším skúškam.
Navyše,interakcia medzi chemikáliami a zariadením je nevyhnutná pre úspech.Vývoj vstrekovacích chemických ventilov musí brať do úvahy chemické vlastnosti a umiestnenie vstrekovacieho ventilu vo vrte.Malo by sa zvážiť zahrnutie skutočných vstrekovacích ventilov ako súčasti testovacieho zariadenia a vykonanie testovania výkonu inhibítora vodného kameňa a konštrukcie ventilu ako súčasť kvalifikačného programu.Na kvalifikáciu inhibítorov vodného kameňa,hlavný dôraz bol predtým kladený na procesné výzvy a inhibíciu rozsahu,ale dobrá inhibícia vodného kameňa závisí od stabilného a nepretržitého vstrekovania.Bez stabilného a nepretržitého vstrekovania sa zvýši potenciál vodného kameňa.Ak je vstrekovací ventil inhibítora vodného kameňa vypustený a nedochádza k vstrekovaniu inhibítora vodného kameňa do prúdu tekutiny,studňa a poistné ventily nie sú chránené pred vodným kameňom, a preto môže byť ohrozená bezpečná výroba.Kvalifikačný postup sa musí okrem procesných problémov a účinnosti kvalifikovaného inhibítora vodného kameňa zaoberať aj problémami súvisiacimi so vstrekovaním inhibítora vodného kameňa.
Nový prístup zahŕňa niekoľko disciplín a je potrebné objasniť spoluprácu medzi disciplínami a príslušné zodpovednosti.V tejto aplikácii systém horného procesu,podmorské šablóny a návrh a dokončenie studní.Multidisciplinárne siete zamerané na vývoj robustných riešení pre chemické vstrekovacie systémy sú dôležité a možno aj cestou k úspechu.Komunikácia medzi rôznymi disciplínami je dôležitá;dôležitá je najmä úzka komunikácia medzi chemikmi, ktorí majú kontrolu nad aplikovanými chemikáliami, a inžiniermi vrtu, ktorí majú kontrolu nad zariadením používaným vo vrte.Pochopiť výzvy rôznych disciplín a učiť sa jeden od druhého je nevyhnutné na pochopenie zložitosti celého procesu.
Záver
● Nepretržité vstrekovanie inhibítora vodného kameňa na ochranu DHS Vor produkčné potrubie je elegantný spôsob ochrany studne pred vodným kameňom
● Riešiť identifikované problémy,sú nasledujúce odporúčania:
● Musí byť vykonaný špeciálny kvalifikačný postup DHCI.
● Spôsob kvalifikácie pre ventily na vstrekovanie chemikálií
● Testovacie a kvalifikačné metódy pre chemickú funkčnosť
● Vývoj metódy
● Testovanie príslušného materiálu
● Multidisciplinárna interakcia, kde je komunikácia medzi rôznymi zapojenými disciplínami kľúčová pre úspech.
Poďakovanie
Autor ďakuje Statoil AS A za povolenie publikovať túto prácu a Bakerovi Hughesovi a Schlumbergerovi za umožnenie použitia obrázku na Obr.
Nomenklatúra
(Ba/Sr)SO4 = síran bárnatý/strontnatý
CaCO3 = uhličitan vápenatý
DHCI = dolná chemická injekcia
DHSV = poistný ventil v hĺbke
napr.=napr
GOR = pomer benzínu
HSE=prostredie ochrany zdravia
HPHT = vysoký tlak vysoká teplota
ID = vnútorný priemer
ie=teda
km = kilometre
mm = milimeter
MEG = mono etylénglykol
mMD = meter nameraná hĺbka
OD = vonkajší priemer
SI = inhibítor vodného kameňa
mTV D = meter celková vertikálna hĺbka
U-rúrka = U v tvare rúrky
VPD = prostriedok na zníženie tlaku pár
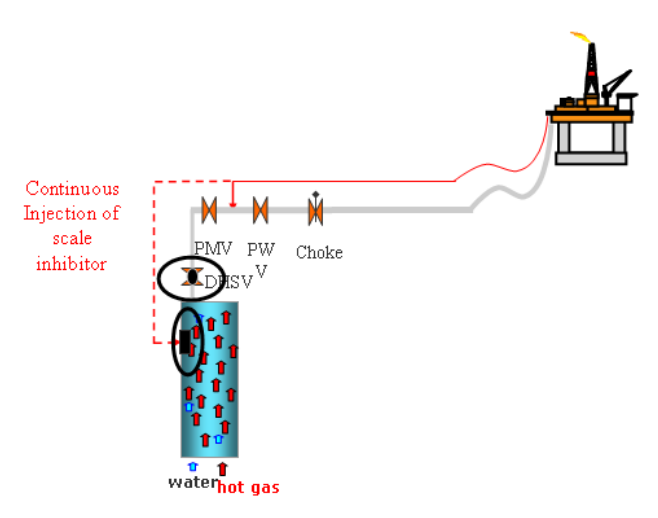
Obrázok 1. Prehľad podmorských a hĺbkových chemických vstrekovacích systémov v atypickej oblasti.Náčrt chemického vstrekovania proti prúdu DHSV a súvisiace očakávané výzvy.DHS V = poistný ventil na zvislej jamke, PWV = procesný krídlový ventil a PM V = procesný hlavný ventil.
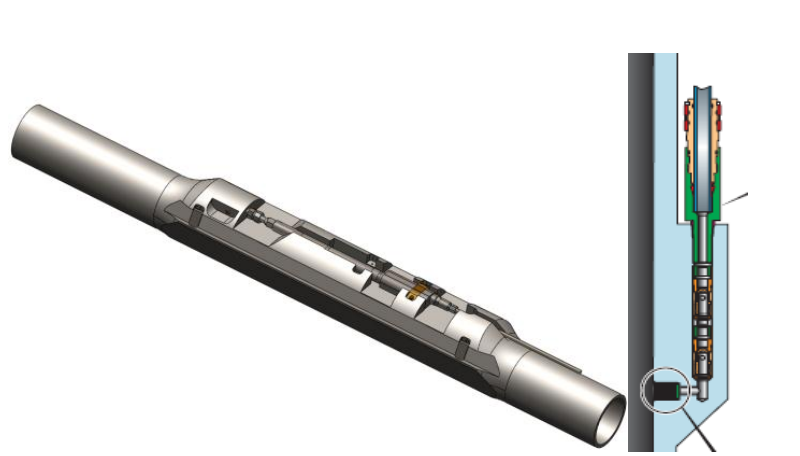
Obrázok 2. Náčrt atypického systému vstrekovania chemikálií s tŕňom a ventilom.Systém je pripojený k povrchovému rozdeľovaču, vedený cez a pripojený k závesu hadičiek na prstencovej strane hadičky.Chemický injektážny tŕň sa tradične umiestňuje hlboko do vrtu s úmyslom poskytnúť chemickú ochranu.
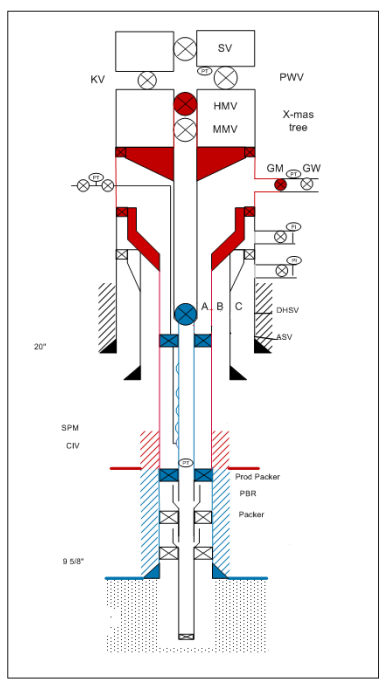
Obrázok 3. Typická schéma bariéry studne,kde modrá farba predstavuje primárnu bariérovú obálku studne;v tomto prípade výrobné potrubie.Červená farba predstavuje sekundárny bariérový obal;puzdro.Na ľavej strane je označená chemická injekcia, čierna čiara s bodom vstrekovania do výrobného potrubia v oblasti označenej červenou (sekundárna bariéra).
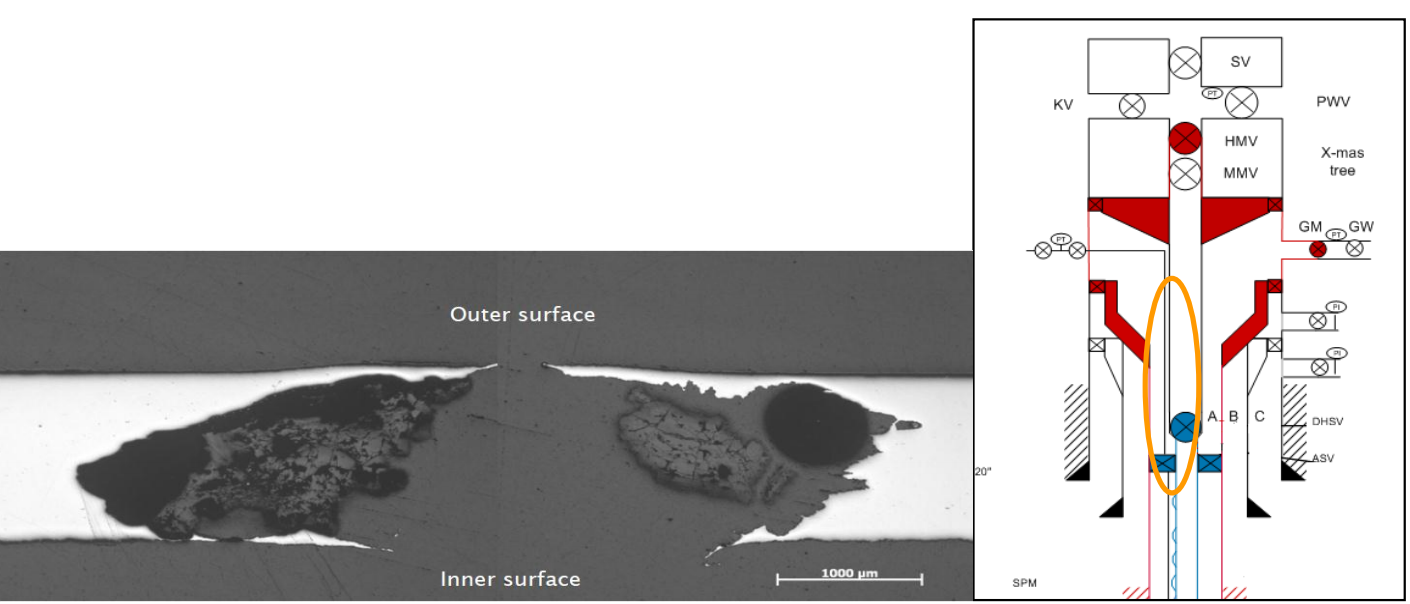
Obrázok 4. Jamkový otvor nájdený v hornej časti 3/8” vstrekovacieho potrubia.Oblasť je znázornená na náčrte atypickej schémy studničnej bariéry, označenej oranžovou elipsou.
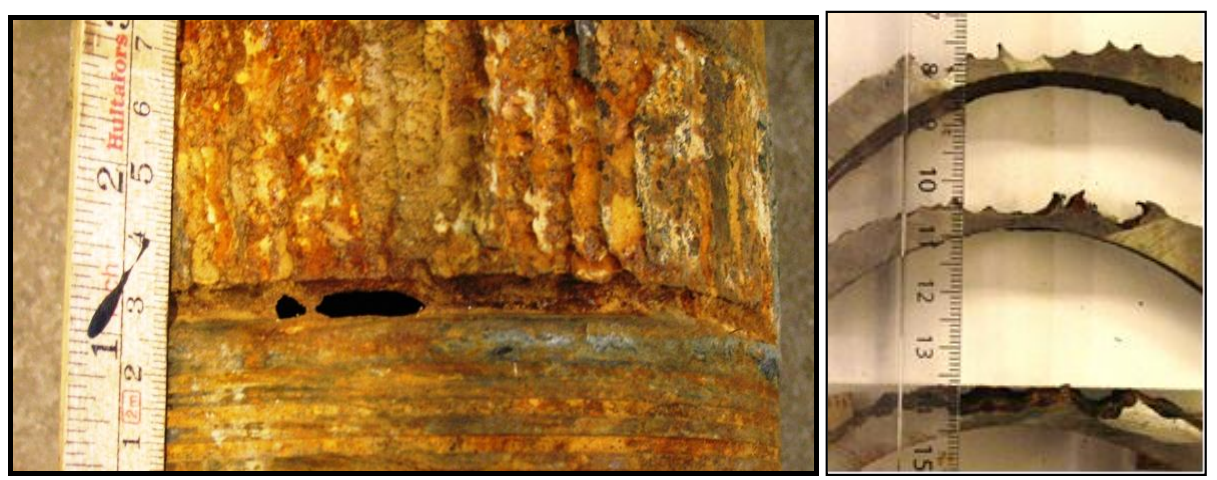
Obrázok 5. Silné napadnutie koróziou na 7” 3% chrómových hadičkách.Obrázok ukazuje napadnutie koróziou po nastriekaní inhibítora vodného kameňa z jamkovej chemickej vstrekovacej linky na výrobné potrubie.
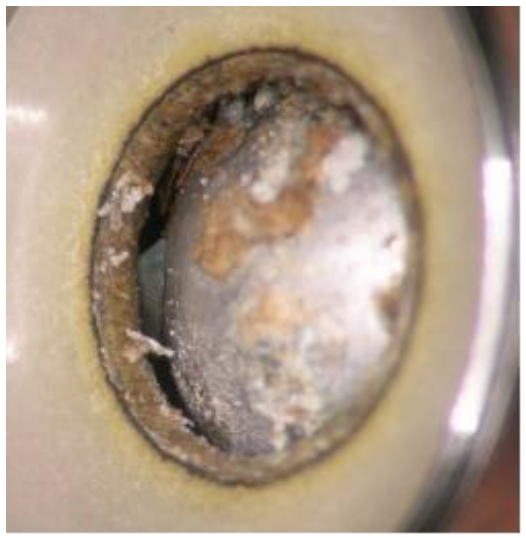
Obrázok 6. Nečistoty nájdené vo ventile vstrekovania chemikálií.Nečistoty v tomto prípade boli kovové hobliny pravdepodobne z procesu inštalácie okrem niektorých belavých úlomkov.Pri skúmaní bielych úlomkov sa ukázalo, že ide o polyméry s podobnou chémiou ako injektovaná chemikália
Čas odoslania: 27. apríla 2022